Colorex SD, dissipative
dpvlink 13997
Properties of the floor covering
Constant conductivity over the entire service life
The unique material construction of Colorex SD ensures constant conductivity over the entire service life of the flooring, regardless of humidity and temperature. In combination with suitable footwear, Colorex EC conducts charges safely through the vein network. Colorex SD not only safely dissipates the charge generated by people, but also reduces the charge at the interface between the sole of the shoe and the floor. This floor meets all ESD standards
Cleanroom suitability
In microelectronics cleanroom environments, even the finest air particles can cause contamination. The consequences are pre-damage and loss of input. As a highly compressed material with a non-porous surface, Colorex SD meets the highest requirements for particle emission behavior and helps to reduce contamination by molecular airborne particles.
Germ and particle-free surface
Meets the highest hygiene requirements thanks to the antimicrobial, compact and non-porous surface. The floor is also characterized by very good resistance to disinfectants.
Resilient
The high-pressure pressed construction is extremely hard-wearing, resistant to high point loads and resistant to static and dynamic loads. It also has excellent chemical resistance.
100% restorable and repairable
Deep and long scratches, holes and burns can be removed effectively and without a trace, without impairing the original properties of the flooring. Visible damage can be repaired by thermal material-in-material welding. To do this, a strip of the same flooring material is heated and worked directly into the damage. After grinding and polishing the repaired area, a homogeneous appearance is restored. Dangerous impurities caused by radionuclides can be removed without leaving any residue.
Care and value retention
Loose dirt can be removed by vacuuming or damp mopping with impregnated disposable cloths. Alternatively, the floor can be spray-cleaned using a single-disc machine with a red pad and spray device with a neutral and wax-free cleaning solution. Clean large areas with a suitable scrubbing machine. Clean the edges manually.
Colorex starts where others stop
Colorex is manufactured using a special production technique. This process gives the material an extremely high and uniform density.
Step 1: Shredding and conductive coating
The sheet material is cut into individual, small “chips”. These are then coated with a conductive substance.
Advantage
- Constant conductivity over the entire service life
- The individual coated chips work as “conductor tracks” and guarantee constant conductivity over the entire service life of the flooring, regardless of the humidity and temperature.
Step 2: High-pressure pressing process
The conductive chips are pressed into thick blocks of material under extremely high pressure and temperature.
Advantage
- High load capacity
- The chips pressed under high pressure form a perfect, homogeneous material composition that can easily withstand high mechanical and dynamic loads over the long term.
Step 3: Splitting and mechanical surface treatment
The homogeneous, pressed blocks are then cut into individual 2.0 mm thick plates.
Advantage
- Can be repaired/rehabilitated, resistant to chemicals
- Cutting the homogeneous slabs enables complete repairability without visual and functional impairment of the floor and - thanks to the highly compacted surface - excellent chemical resistance
Colorex fully bonded
Conductive installation guarantees that unwanted electrostatic charges can flow through the dense network of fine conductive tracks through the entire panel thickness. The charges are safely dissipated by the conductive adhesive and the copper strips. If a conductive floor is not required, Colorex can also be laid with normal adhesive as a non-conductive variant. In order to meet the highest hygiene requirements, it is recommended that Colorex is thermally welded in the same color.
Dissipative vinyl floor covering
According to DIN EN 649, homogeneous
Suitable for areas of use with the following requirements:
- Ground resistance RE according to DIN EN 1081: < 108 Ohm
- Ground resistance RE according to IEC 6-1340: 106 Ohm to ≤ 108 Ohm (DIF)
Properties:
- Without chemical antistatic agents
- Conductive back coating
- Guaranteed electrical properties over the entire service life
- High-pressure pressed and cut from the block
- Low plasticizer content
- Suitable for chair castors in accordance with DIN EN 12529 type W
Fire protection and resistance:
Fire behavior:
- DIN 4102-1: Class B1/Q1 (low flammability, low smoke emission)
- EN 13501-1: Class Bfl-S1
Chemical resistance according to EN 423
Suitable for abrasive cleaning technology
Technical data:
Thickness: 2.0 mm
Tile size: 615 × 615 mm
Surface: veined, smooth
Laying:
Glue to a fully leveled substrate with conductive dispersion adhesive (< 3 × 105 Ohm).
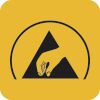