Colorex PLUS EC interlocking system
dpvlink 13999
Highly conductive and flexible flooring system
Colorex Plus EC is the highly conductive solution for maximum safety in preventing electrostatic charges and meets the latest international standards. The flooring has an earth bleeder resistance of 5 x 10 4 -1 x 10 6 Ω and is suitable for grounding people via the man-shoe-floor system (IEC 61340-4-5) to protect electronic components and equipment from personal discharges. The conductive vinyl puzzle tiles of the Colorex Plus EC ESD flooring system are particularly suitable for ESD areas, operating theaters/intensive care units, cleanrooms, explosion-proof rooms and for use in the electrical and pharmaceutical industries.
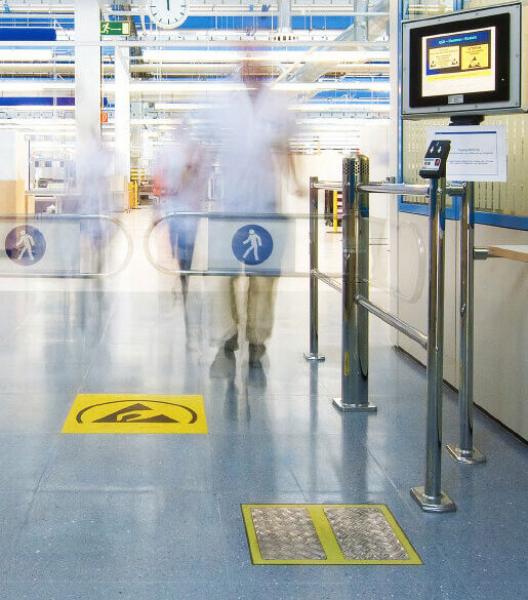
Properties of the floor covering
Constant conductivity over the entire service life
The unique material construction of Colorex SD ensures constant conductivity over the entire service life of the flooring, regardless of humidity and temperature. In combination with suitable footwear, Colorex EC conducts charges safely through the vein network. Colorex SD not only safely dissipates the charge generated by people, but also reduces the charge at the interface between the sole of the shoe and the floor. This floor meets all ESD standards
Cleanroom suitability
In microelectronics cleanroom environments, even the finest air particles can cause contamination. The consequences are pre-damage and loss of input. As a highly compressed material with a non-porous surface, Colorex SD meets the highest requirements for particle emission behavior and helps to reduce contamination by molecular airborne particles.
Germ and particle-free surface
Meets the highest hygiene requirements thanks to the antimicrobial, compact and non-porous surface. The floor is also characterized by very good resistance to disinfectants.
Resilient
The high-pressure pressed construction is extremely hard-wearing, resistant to high point loads and resistant to static and dynamic loads. It also has excellent chemical resistance.
100% restorable and repairable
Deep and long scratches, holes and burns can be removed effectively and without a trace, without impairing the original properties of the flooring. Visible damage can be repaired by thermal material-in-material welding. To do this, a strip of the same flooring material is heated and worked directly into the damage. After grinding and polishing the repaired area, a homogeneous appearance is restored. Dangerous impurities caused by radionuclides can be removed without leaving any residue.
Care and value retention
Loose dirt can be removed by vacuuming or damp mopping with impregnated disposable cloths. Alternatively, the floor can be spray-cleaned using a single-disc machine with a red pad and spray device with a neutral and wax-free cleaning solution. Clean large areas with a suitable scrubbing machine. Clean the edges manually.
Colorex starts where others stop
Colorex is manufactured using a special production technique. This process gives the material an extremely high and uniform density.
Step 1: Shredding and conductive coating
The sheet material is cut into individual, small “chips”. These are then coated with a conductive substance.
Advantage
- Constant conductivity over the entire service life
- The individual coated chips work as “conductor tracks” and guarantee constant conductivity over the entire service life of the flooring, regardless of the humidity and temperature.
Step 2: High-pressure pressing process
The conductive chips are pressed into thick blocks of material under extremely high pressure and temperature.
Advantage
- High load capacity
- The chips pressed under high pressure form a perfect, homogeneous material composition that can easily withstand high mechanical and dynamic loads over the long term.
Step 3: Splitting and mechanical surface treatment
The homogeneous, pressed blocks are then cut into individual 2.0 mm thick plates.
Advantage
- Can be repaired/rehabilitated, resistant to chemicals
- Cutting the homogeneous slabs enables complete repairability without visual and functional impairment of the floor and - thanks to the highly compacted surface - excellent chemical resistance
Technical dataCE sign | EN 14014 | conform |
Surface |
| smooth |
Total thickness | EN ISO 24346 | 2.0 mm |
Trade class | EN ISO 10874 | 34 very strong |
Industrial class | EN ISO 10874 | 43 strong |
Size (without dovetails) | EN ISO 24342 | 615 x 615 mm |
Surface weight | EN ISO 23997 | 3.2 kg/m² |
Plate weight |
| 4.6 kg |
Fire behavior | EN 13501-1 | Bfl -S1, G, CS |
Thermal conductivity | EN 12524 | 0.25 W/(m·k) |
Slip resistance | DIN 51130 | R9 |
| bfu/bpa/upi R 9729 | GS1 |
Resistance to castor wheels | ISO 4918 | suitable type W |
Thermal dilation coefficient |
| 0.07 mm/m°C |
Electrical bleeder resistance | IEC 61340-4-1 | 1 x 106 ≤ R ≤ 108 Ω |
| ESD STM7.1 |
|
Insulation resistance | DIN VDE 0100 | ≥ 50 kΩ |
Electrical system resistance with ESD shoes | IEC 61340-4-5 | R ≤ 1 x 109 Ω |
| ESD STM97.1 |
|
Walk-on charge with ESD shoes (typical value) | IEC 61340-4-5 | < 100 V ~ 40 V |
| ESD STM97.2 |
|
Dimension stability | EN ISO 23999 | ≤ 0,05% |
Residual indentation behavior (typical value) | EN ISO 24343-1 | ≤ 0.10 mm ~ 0.02 mm |
Impact sound improvement | EN ISO 140-8 | 2 dB |
Light fastness | EN ISO 105-B02 | ≤ 6 |
Resistance to load | Lift trucks and forklift trucks: Total weight up to 2.5 t and with pneumatic tires 5 t; Static: 50 kg/cm³ - Dynamic 90 kg/cm³ | |
Chemical effects | EN ISO 26987 | very good |
Cleanroom emissions | IDEMA M11-99 | total < 1 μg/cm2 |
Cleanroom particle emissions | IDEMA 14644-1 | ISO 4 |
Recycling part | up to 95% recycled content in the back construction |